What are the challenges associated with identifying a vibration motor intermittent flex or motor fault?
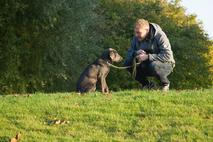
What are the challenges associated with identifying a vibration motor intermittent flex or motor fault?
When dealing with the issue of a vibration motor intermittent flex or motor fault, I often find myself facing a series of perplexing challenges. It’s incredibly frustrating because the symptoms aren’t always consistent, making it difficult to pinpoint the exact nature of the problem. Sometimes the motor runs smoothly, and at other times, it may fail entirely or behave erratically. This sporadic malfunctionality disrupts the regular operation of my device and leaves me questioning whether the issue lies with the motor itself or the flexible components connected to it.
Additionally, the intermittent nature of the fault means that it can sometimes appear to resolve itself temporarily, only to reoccur unexpectedly. This inconsistency is maddening and makes systematic troubleshooting almost impossible. I often worry that my attempts to identify the issue might miss the windows of malfunction, leading to misleading conclusions.
To further complicate matters, these faults can arise from a variety of underlying causes, such as physical wear and tear, loose connections, or even subtle manufacturing defects. The complexity of modern devices means that a problem in one area could potentially cascade, creating a multifaceted dilemma that is overwhelming to diagnose. The uncertainty of dealing with a vibration motor intermittent flex or motor fault has made it one of the more challenging technical issues I’ve faced.
5 Answers
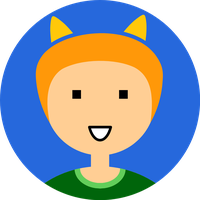
When I had to resolve a vibration motor intermittent flex or motor fault, my approach combined careful observation with rigorous testing. Firstly, I operated the device over a prolonged period to understand when the fault occurred. This long-term observation helped me spot patterns that short tests missed. Cleaning all electrical contacts with isopropyl alcohol was crucial for maintaining consistent connections. Testing components individually helped isolate the problem, like running the motor directly from a power source to determine if the fault was with the motor itself.
Lastly, applying stress to various parts of the circuit revealed weak points. By gently flexing cables while the motor was running, I could detect breaks in continuity that weren’t obvious at the outset.
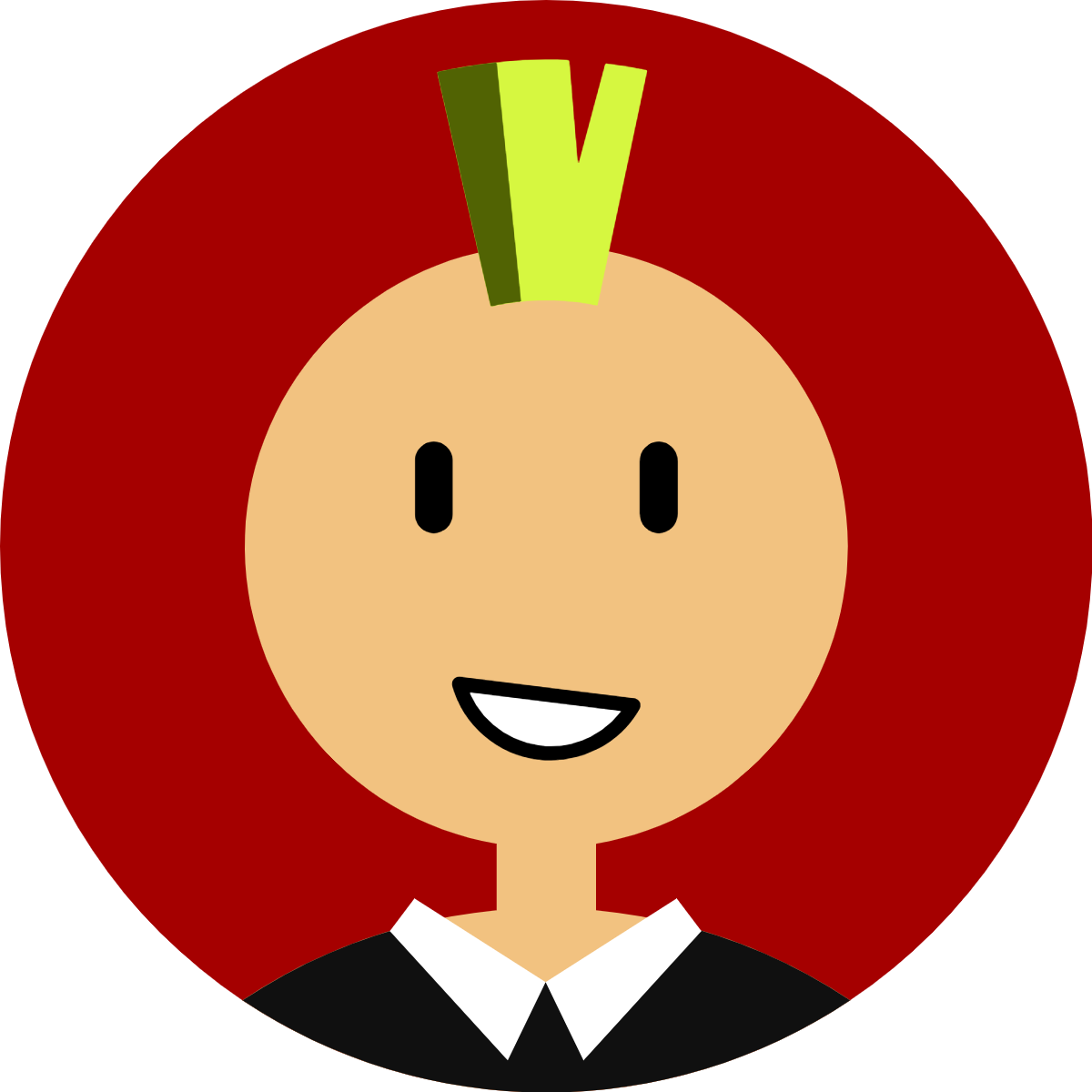
To troubleshoot a vibration motor intermittent flex or motor fault, I start with a thorough visual inspection. By checking the motor and all its connections closely, I often find loose wires or other obvious signs of wear and tear. Feeling the wires and securing any loose connections can resolve many issues. Next, examining the flex cables for any physical damage helps, as repeated motions can cause these cables to wear out or break over time.
Using a multimeter to check continuity and resistance across motor terminals and flex cables is essential. This tool helps identify hidden breaks or shorts that are not visible. Monitoring the power supply is also crucial; ensuring the motor receives a consistent voltage can prevent erratic behavior. Lastly, updating the firmware or software controlling the motor often resolves motor issues caused by software glitches.
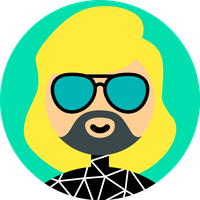
To address an intermittent fault with the vibration motor, I adopted a structured strategy that involved a series of checks and tests:
1. Ensuring all connections were secure and debris-free helped avoid simple faults.
2. Double-checking the power supply voltage and current ensured the motor wasn’t being over- or under-powered.
3. Conducting a thorough inspection of the motor revealed any signs of physical wear or damage.
4. Running the motor under different loads helped identify faults that only appeared under stress.
5. Making sure the device’s software and firmware were up to date avoided any software-related issues.
Following these steps systematically helped me narrow down and resolve the intermittent fault.
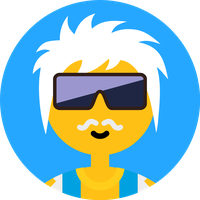
Identifying the problem with a vibration motor often boils down to electrical and mechanical checks. I ensure all electrical connections are secure, as even a slightly loose wire can create massive headaches. Firmly tugging on each connector helps verify stability. I also examine mechanical parts such as bearings or screws for wear or misalignment. Vibrations over time can cause these parts to shift and degrade performance.
Another factor to consider is environmental conditions like temperature and humidity. These can affect the motor’s performance by causing materials to expand or contract. Addressing every potential issue methodically helped me narrow down where the fault lay and eventually fix the problem.
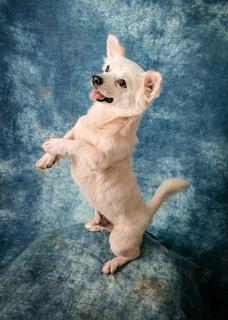
Facing an intermittent vibration motor fault, I’ve learned that a methodical approach is key. Initially, I conduct a visual and tactile examination of the motor and flex cables, looking for any evident physical issues. Diagnostic tools come next, where I use continuity checks and stress tests under various conditions to pinpoint issues. Observing patterns in the fault’s occurrence helps to identify specific scenarios that cause the problem, guiding me to focus on potential solutions effectively.