What challenges are commonly faced during a Google Pixel 6a screen repair? What is this for part?
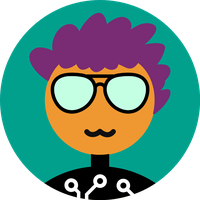
What challenges are commonly faced during a Google Pixel 6a screen repair? What is this for part?
When I was trying to fix my Google Pixel 6a screen, it became evident that the task was more complex than I initially thought. While I expected a simple procedure, I encountered several challenges that made the repair process difficult. The first issue was identifying the exact parts and tools needed. The screen assembly for the Google Pixel 6a includes specific components that are not always compatible with parts from other models or aftermarket options. Disconnecting internal components without causing further damage was another hurdle. The delicate nature of the device’s internals meant that even a slight misstep could lead to more significant problems.
Additionally, there were concerns about maintaining the phone’s waterproof integrity after the repair. I wasn’t sure if my amateur repair skills would be sufficient to ensure the phone remained protected from water and dust. Another challenge was the calibration of the new screen to function correctly with the phone’s hardware and software, which was something I hadn’t anticipated. It’s clear that careful consideration and a good understanding of what each part does are crucial for a successful Google Pixel 6a screen repair. This experience left me wondering if DIY repairs are worth the risk, given the potential for creating more issues.
4 Answers
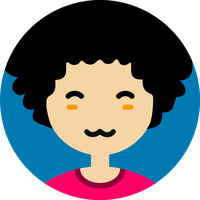
- I found it really hard to source genuine parts. The market is flooded with counterfeit and low-quality screens that don’t perform well.
- Disconnecting the internal components posed a big risk. These parts are delicate, and I had to be exceedingly careful to avoid causing irreversible damage.
- Ensuring that the phone retained its waterproof nature was another struggle. I soon realized that without the right sealing equipment, achieving this at home is highly impractical.
- The software didn’t recognize the new screen immediately, and I had to troubleshoot extensively to get it to work properly, which was frustrating.
- The lack of immediate professional assistance meant I had to rely on online tutorials, which were not always clear or consistent.
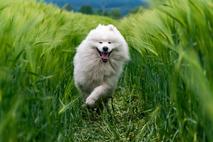
- One of the main challenges I faced was sourcing the correct replacement screen. Not all screens available online are genuine or of high quality. Some cheaper options didn’t align perfectly with the phone’s chassis, leading to gaps and improper fitting. To avoid this, I had to meticulously check the specifications and ensure compatibility, which was time-consuming.
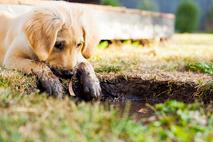
- When replacing the screen, I struggled with identifying the parts. The screen assembly is intricate, and missing a step in removing connectors could ruin the phone.
- Keeping track of tiny screws was another headache. Using a magnetic mat helped, but it’s still easy to mix up which screws went where.
- Lastly, the reassembly process demanded precision. Ensuring that cables and components were aligned correctly, without applying too much pressure, was nerve-wracking.
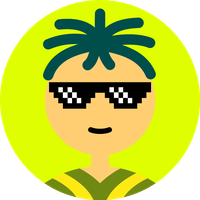
- Sourcing reliable parts was a major issue. I discovered that many aftermarket screens varied in quality, and it was difficult to find one that matched the original’s responsiveness and clarity.
- During the repair, handling the delicate internal components without proper tools proved challenging. The connectors and ribbons are particularly fragile, and I was constantly worried about tearing them accidentally.
- Another significant challenge was reassembling the phone without compromising its waterproof integrity. Without professional sealing tools, ensuring the device remained water-resistant seemed almost impossible.